國(guó)內(nèi)硅料企業(yè)紛紛開啟新一輪的擴(kuò)產(chǎn)大潮。對(duì)于多晶硅生產(chǎn)的兩大技術(shù)路線,市場(chǎng)出現(xiàn)兩級(jí)分化。改良西門子法還是流化床法,又一次成為爭(zhēng)論的焦點(diǎn)。由于多晶硅的重要性,技術(shù)路線選擇,這次路線之爭(zhēng)無(wú)不牽動(dòng)廣大新能源投資者的神經(jīng)。
早在上世紀(jì)五六十年代,多晶硅生產(chǎn)的兩大技術(shù)路線相繼問(wèn)世,其中西門子法通過(guò)多次技術(shù)迭代一直引領(lǐng)行業(yè)前行,成為世界的主流路線,而流化床法作為第二技術(shù)路線也在持續(xù)進(jìn)步。
在“雙碳目標(biāo)”的背景下,光伏成為可再生能源的主力,這場(chǎng)跨越世紀(jì)之爭(zhēng)的答案也越發(fā)清晰可見。
01為什么多晶硅的技術(shù)路線如此重要?
【1】多晶硅的行業(yè)地位
能源革命的浪潮之下,光伏的重要性目前已再無(wú)分歧;從產(chǎn)業(yè)鏈的視角來(lái)看,多晶硅作為光伏產(chǎn)業(yè)的上游原材料,其在整個(gè)光伏產(chǎn)業(yè)中占有舉足輕重的地位。同時(shí)多晶硅也是集成電路最為關(guān)鍵的基礎(chǔ)原材料。
圖1:光伏產(chǎn)業(yè)鏈?zhǔn)疽鈭D,資料來(lái)源:新疆大全招股說(shuō)明書
首先,多晶硅的成本與光伏發(fā)電系統(tǒng)的成本直接掛鉤。早在2014年,國(guó)家發(fā)改委能源研究所等研究機(jī)構(gòu)發(fā)布的《中國(guó)可再生能源發(fā)展路線圖2050》就提出,2025年光伏要能實(shí)現(xiàn)全面平價(jià)上網(wǎng),那成本下降就成了光伏產(chǎn)業(yè)進(jìn)步的不竭動(dòng)力,而其中的大頭就是硅料。發(fā)展初期,多晶硅的成本曾一度占太陽(yáng)電池的近50%。
回溯光伏過(guò)去十余年的發(fā)展,光伏成本從50元/W下降到了4元/W左右,多晶硅環(huán)節(jié)的持續(xù)降本為光伏平價(jià)上網(wǎng)做出了巨大的歷史貢獻(xiàn)。
圖2:產(chǎn)業(yè)鏈各環(huán)節(jié)價(jià)格(元/W、元/kg),資料來(lái)源:中國(guó)有色金屬工業(yè)協(xié)會(huì)硅業(yè)分會(huì),國(guó)信證券
根據(jù)BP發(fā)布的2020年能源展望數(shù)據(jù),到2050年,光伏發(fā)電的成本較2018年還能下降70%。這必然要求光伏產(chǎn)業(yè)鏈各個(gè)環(huán)節(jié)共同努力,多晶硅最為材料源頭,將長(zhǎng)期擔(dān)當(dāng)降本增效的重任。
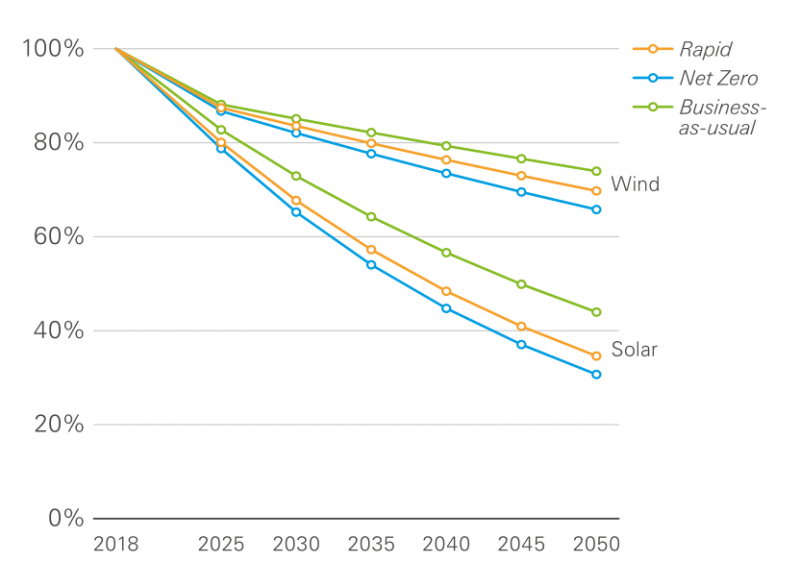
圖3:未來(lái)30年光伏成本下降曲線,資料來(lái)源:BP Energy
其次,多晶硅的質(zhì)量的提升促進(jìn)光伏的技術(shù)進(jìn)步和國(guó)產(chǎn)替代。自2018年初開始,單晶硅片產(chǎn)能規(guī)模快速擴(kuò)張,成為行業(yè)主流,為滿足下游需求,國(guó)內(nèi)多晶硅企業(yè)在積極擴(kuò)張的同時(shí),也加速了光伏級(jí)硅料品質(zhì)的提升。目前通威股份、新疆大全的特級(jí)料占比均超過(guò)90%。
與此同時(shí),我國(guó)多晶硅料品質(zhì)的提升,對(duì)于硅料進(jìn)口依賴的下降功不可沒(méi),根據(jù)硅業(yè)分會(huì)的數(shù)據(jù),硅料進(jìn)口占比已經(jīng)從2016年的42.1%下降至2020年的20.2%。2021年1月,通威股份已實(shí)現(xiàn)N型硅料的批量生產(chǎn)。
時(shí)至今日,我國(guó)多晶硅產(chǎn)業(yè)已取得了長(zhǎng)足進(jìn)步,從產(chǎn)業(yè)化早期的幾乎完全依靠進(jìn)口到目前產(chǎn)量已占全球的三分之二,國(guó)內(nèi)的產(chǎn)銷規(guī)模已經(jīng)位居全球首位。但在太陽(yáng)能光伏平價(jià)上網(wǎng)的倒逼下,多晶硅降本增量之路還在繼續(xù)。
第三,終端光伏裝機(jī)需求帶來(lái)多晶硅的增長(zhǎng)
多晶硅也是一將功臣萬(wàn)骨枯的行業(yè),打的頭破血流,最終呈現(xiàn)強(qiáng)者恒強(qiáng),兩極分化的局面。頭部企業(yè)憑借技術(shù)和成本優(yōu)勢(shì)維持較高水平的產(chǎn)能利用率。如通威股份,2017-2019 年產(chǎn)能利用率分別為93.70%、96.38%、92.46%,2020年上半年達(dá)到了116%。而中小企業(yè)產(chǎn)能利用率較低,部分企業(yè)由于投產(chǎn)較早、設(shè)備陳舊、規(guī)模較小,已逐步停產(chǎn)。
據(jù)《中國(guó)能源報(bào)》統(tǒng)計(jì),國(guó)內(nèi)在產(chǎn)高純晶硅企業(yè)數(shù)量由2018年初的24家,減少至2019年初的18家,再縮減至2019年底的12家。
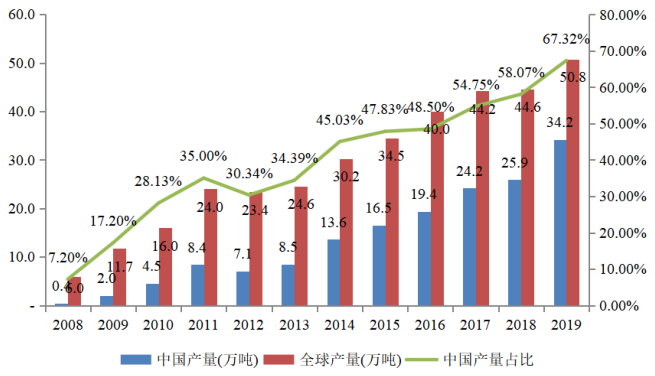
圖4:2008-2019年中國(guó)多晶硅產(chǎn)量及占全球產(chǎn)量的比重,資料來(lái)源:中國(guó)光伏行業(yè)協(xié)會(huì),新疆大全招股書
【2】多晶硅的生產(chǎn)是門技術(shù)活
跟鋰電池行業(yè)的上游原材料不同,多晶硅料具有高載能、重資產(chǎn)、擴(kuò)產(chǎn)周期長(zhǎng)、技術(shù)壁壘高的多重特點(diǎn)。所以多晶硅看似工業(yè)標(biāo)準(zhǔn)品,實(shí)際上更多的屬性是化工品。正因?yàn)榇?,多晶硅的技術(shù)能力是衡量多晶硅企業(yè)的硬核能力之一。
按純度要求及用途不同,可以將多晶硅分為太陽(yáng)能級(jí)多晶硅和電子級(jí)多晶硅,太陽(yáng)能級(jí)多晶硅主要用于太陽(yáng)能電池的生產(chǎn)制造,而電子級(jí)多晶硅作為主要的半導(dǎo)體電子材料,廣泛應(yīng)用于電子信息領(lǐng)域。
太陽(yáng)能級(jí)多晶硅對(duì)雜質(zhì)有嚴(yán)格的要求,通常要求其中雜質(zhì)總含量低于10-6,即多晶硅的純度需達(dá)到99.9999%以上。而電子級(jí)多晶硅可以說(shuō)是技術(shù)巔峰,其純度要求高達(dá)99.999999999%(不用數(shù)了,小數(shù)點(diǎn)后面是9個(gè)9),相當(dāng)于1000噸的電子級(jí)多晶硅中總的雜質(zhì)含量不到一?;ㄉ字亓康?%。所以世界范圍內(nèi)能夠生產(chǎn)電子級(jí)多晶硅產(chǎn)品的企業(yè)屈指可數(shù),電子級(jí)多晶硅成為行業(yè)高地。
總的來(lái)說(shuō),高純多晶硅的生產(chǎn)不是煤炭那種簡(jiǎn)單粗暴只拼產(chǎn)能的行業(yè),它是光伏產(chǎn)業(yè)鏈中技術(shù)含量較高的環(huán)節(jié),加上投資大,風(fēng)險(xiǎn)高。目前國(guó)內(nèi)隆基、中環(huán)等垂直一體化的企業(yè)也沒(méi)有直接下場(chǎng),而是采取參股的方式參與到多晶硅生產(chǎn)。
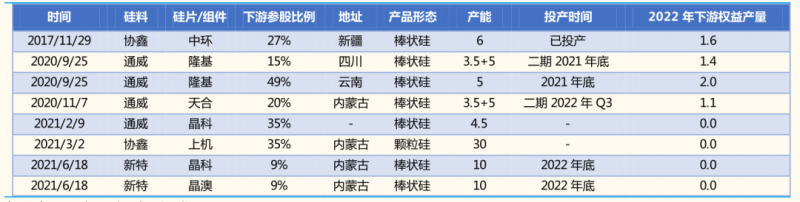
圖5:下游企業(yè)通過(guò)參股方式綁定頭部多晶硅企業(yè)(萬(wàn)噸),資料來(lái)源:各公司公告,國(guó)金證券
02“一大一小”技術(shù)路線
【1】改良西門子法
對(duì)于光伏業(yè)內(nèi)人士而言,西門子法是再熟悉不過(guò)了,這是目前國(guó)內(nèi)外最普遍也是最成熟的方法。根據(jù)中國(guó)光伏行業(yè)協(xié)會(huì)的數(shù)據(jù),2019年全球多晶硅產(chǎn)量中采用改良西門子法生產(chǎn)的占比高達(dá)97.8%;我國(guó)也類似,2020年國(guó)內(nèi)采用改良西門子法生產(chǎn)的多晶硅約占全國(guó)總產(chǎn)量的97.2%。
今天成熟的改良西門子法最早由德國(guó)西門子公司在1955年發(fā)明,在過(guò)去60多年中,業(yè)內(nèi)參與者不停的對(duì)西門子法進(jìn)行技術(shù)優(yōu)化和提升,已經(jīng)改良到了第三代。其優(yōu)點(diǎn)已經(jīng)非常突出。目前全球前十硅料生產(chǎn)企業(yè)的技術(shù)路線都以改良西門子法為主。

圖6:全球前十硅料生產(chǎn)企業(yè),資料來(lái)源:國(guó)信證券
縱觀全球多晶硅的發(fā)展歷史,基本上是和西門子法技術(shù)路線的技術(shù)進(jìn)步同步的。
具體而言,還原爐的材料從石英玻璃發(fā)展到金屬再到不銹鋼,其內(nèi)部的棒數(shù)也逐漸從1對(duì)棒、3對(duì)棒逐漸提升到48對(duì)棒以上的大型還原爐,還原爐產(chǎn)量已從1975年的單爐40噸/年,提升至現(xiàn)在600噸/年的水平。
多晶硅技術(shù)的進(jìn)步已經(jīng)和規(guī)模的擴(kuò)大形成正向循環(huán),收益規(guī)模大型化、技術(shù)優(yōu)化,改良西門子法多晶硅單位產(chǎn)能投資成本大幅下降,多晶硅生產(chǎn)線投資成本從2008年千噸投資成本約為7億元~10億元降到現(xiàn)在的1億元/千噸以下。
根據(jù)工業(yè)發(fā)展規(guī)律,未來(lái)隨著規(guī)模產(chǎn)量的繼續(xù)擴(kuò)大,改良西門子法的競(jìng)爭(zhēng)能力將會(huì)進(jìn)一步強(qiáng)化,主流工藝地位進(jìn)一步穩(wěn)固。
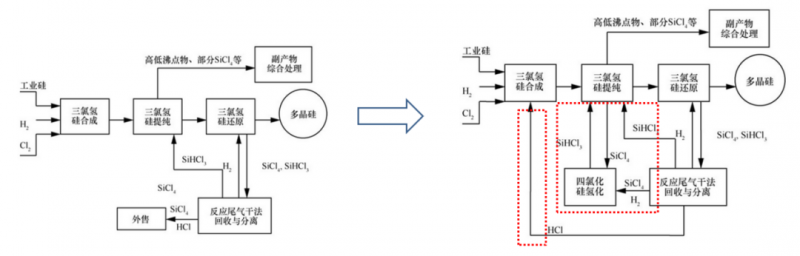
圖7:西門子法生產(chǎn)工藝,資料來(lái)源:《當(dāng)代多晶硅產(chǎn)業(yè)發(fā)展概論》
【2】流化床法——現(xiàn)實(shí)與理想的差距
下面敲重點(diǎn),講講最近備受關(guān)注的流化床法,其實(shí)長(zhǎng)期關(guān)注光伏行業(yè)的人知道,西門子法的應(yīng)于一直遠(yuǎn)大于流化床法。但并不新鮮的流化床法之所以又引起大家的注意源于協(xié)鑫,疊加光伏這個(gè)黃金賽道,其核心要義就是降低成本,所以每個(gè)更降本扯上關(guān)系的新技術(shù)勢(shì)必都讓市場(chǎng)很亢奮。
在我們長(zhǎng)期關(guān)注的動(dòng)力電池領(lǐng)域,也有類似的例子。今年年初,廣汽就曾發(fā)布“石墨烯電池”表示具備6C快充能力,最快8分鐘就能充電至80%,此舉引來(lái)不少吃瓜群眾圍觀。同樣的例子還有特斯拉的4680圓柱電池,這還尚未量產(chǎn),相關(guān)板塊已經(jīng)漲了一輪。
回到流化床法上,最早是美國(guó)聯(lián)碳公司在1952年開發(fā)出將硅烷分解沉積在固定床上硅顆粒表面的技術(shù),這也是流化床技術(shù)最早的雛形,數(shù)年之后,杜邦公司在1961年申請(qǐng)了使用三氯氫硅為原料在流化床內(nèi)生產(chǎn)顆粒硅的專利,標(biāo)志著流化床法正式面世。
同樣師出名門,但流化床法的工業(yè)化之路異常艱辛,難有大為。西門子法經(jīng)過(guò)多次技術(shù)迭代已然成為多晶硅企業(yè)的主菜,流化床法雖有進(jìn)步,卻難于大規(guī)模量產(chǎn),長(zhǎng)期作為配菜。
那么問(wèn)題來(lái)了,流化床法比西門子法晚了6年,但對(duì)于60余年的時(shí)間跨度,可以說(shuō)兩者是處在同一起跑線。為什么流化床法此前一直備受冷落?
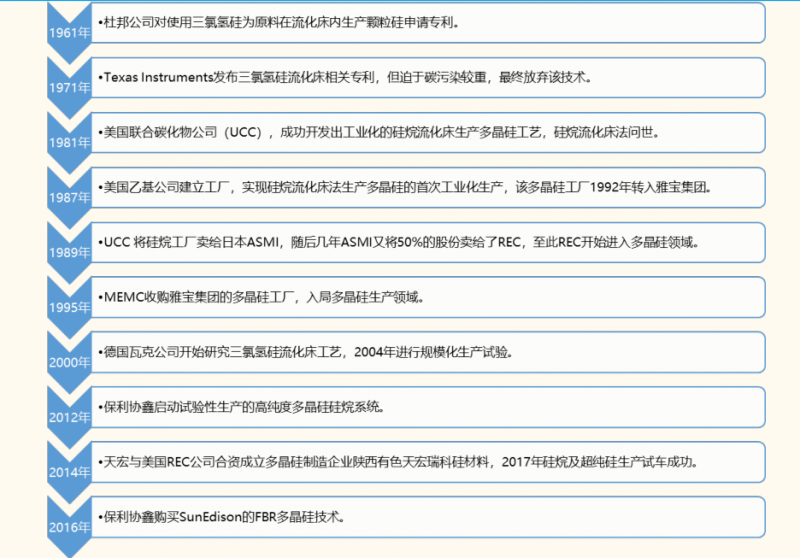
圖8:流化床法制備多晶硅技術(shù)的發(fā)展歷程,資料來(lái)源:《當(dāng)代多晶硅產(chǎn)業(yè)發(fā)展概論》,國(guó)金證券
1) 基本原理
流化床法的主要原理是將硅烷用氫氣作為載體,像氣流一樣從流化床反應(yīng)器底部注入,然后上升到中間加熱區(qū)反應(yīng),因?yàn)橛械撞窟M(jìn)料時(shí)候的氣流源源不斷的進(jìn)入,可以讓反應(yīng)器內(nèi)的籽晶沸騰起來(lái),處于懸浮狀態(tài),注入的硅烷等原料和氫氣在加熱區(qū)發(fā)生反應(yīng),然后,隨著反應(yīng)的進(jìn)行,硅逐漸沉積在懸浮狀態(tài)的硅籽晶上,籽晶顆粒不斷地生長(zhǎng),長(zhǎng)大到足夠重量的時(shí)候,硅顆粒沉降到反應(yīng)器的底部,排出的就是顆粒硅。
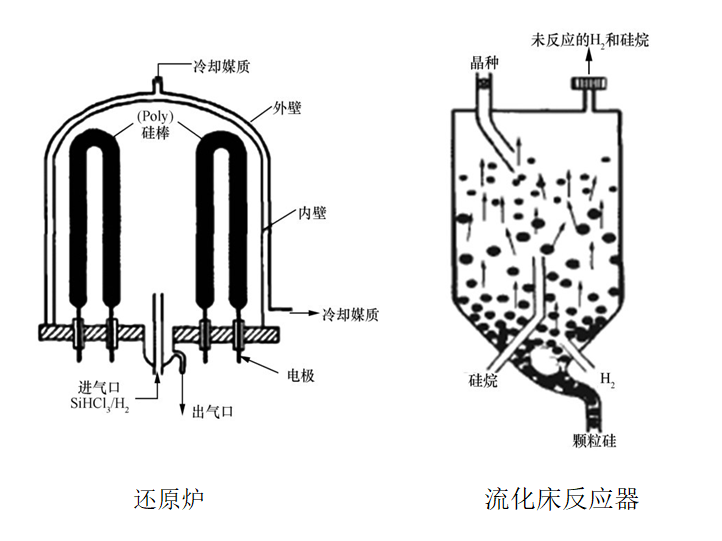
圖9:改良西門子法與流化床法核心設(shè)備對(duì)比,資料來(lái)源:《當(dāng)代多晶硅產(chǎn)業(yè)發(fā)展概論》
2) 令人著迷的優(yōu)勢(shì)
相對(duì)改良西門子法,流化床法的最大優(yōu)勢(shì)主要體現(xiàn)在流化床反應(yīng)器上。
其一,由于底部進(jìn)料的氣流存在,硅籽晶處在懸浮狀態(tài),可提供更大的反應(yīng)面積,從而獲得較高的反應(yīng)效率,硅顆粒生長(zhǎng)速度更快;同時(shí),流化床反應(yīng)器內(nèi)是體和固體接觸好,熱能傳遞效率高,電耗自然就降下來(lái)了。能耗相對(duì)較低。在于參加反應(yīng)的顆粒硅晶種表面積大,沉積速度(生長(zhǎng)速度)大幅提高,故生產(chǎn)效率高,大大減少了能源消耗,降低了成本。
其二,從上圖中可以看到,流化床反應(yīng)器是上下加料,硅烷和氫氣從底部注入,硅籽晶從頂部加料,生產(chǎn)的硅顆粒從底部排出,可以做到連續(xù)生產(chǎn),提高生產(chǎn)效率。
其三,流化床法主要從硅烷作為原料,其反應(yīng)的溫度低,分解較為完全,使系統(tǒng)的尾氣回收壓力大為降低,約700攝氏度以下,而改良西門子法的反應(yīng)溫度高達(dá)1050攝氏度,單從這方面看,流化床法就比后者省電不少。
其四,流化床法的的副反應(yīng)較少,可縮短尾氣回收流程,減少投資成本。
其五,流化床法的產(chǎn)品就是顆粒硅,在下一加工環(huán)節(jié)就可以直接使用,可滿足連續(xù)投料拉晶工藝的發(fā)展。不需要再像改良西門子法那樣破碎。
講了這么多,有人要坐不住了,你說(shuō)流化床法這么多優(yōu)點(diǎn),處處蓋過(guò)西門子法,為什么歷史發(fā)展緩慢,且未來(lái)難有作為?我們的結(jié)論是,你的優(yōu)勢(shì),也許就是你的劣勢(shì)。
3) “致命”的劣勢(shì)
不看好改良西門子法的投資者一般的觀點(diǎn)就是,能耗大、副產(chǎn)物多,但是這些是可以通過(guò)技術(shù)改進(jìn),逐步改善的。
在能耗方面,多晶硅企業(yè)曾被戴上“高能耗”的帽子。今天多晶硅生產(chǎn)全流程綜合電耗已經(jīng)從2009年的200kwh/kg-Si降低至2020年的60kwh/kg-Si,降幅達(dá)到70%,有些頭部企業(yè)甚至已經(jīng)降到50kwh/kg-Si以下的水平,同時(shí)水耗則基本維持在67 kg/kg.Si左右。
同時(shí),值得注意的是,除了老生常談的電耗和水耗,能耗的綜合考慮還需要加上蒸汽消耗。不同于改良西門子法的副產(chǎn)蒸汽用于發(fā)電,蒸汽單耗基本上已經(jīng)下降到0,硅烷流化床法還會(huì)使用到蒸汽、天然氣等,所以這部分有關(guān)蒸汽的25kg/kg.Si左右的能耗僅在生產(chǎn)顆粒硅的時(shí)候會(huì)產(chǎn)生,需要綜合考慮進(jìn)去,最后,綜合能耗算下來(lái),兩種技術(shù)的能耗差距并不大。
在副產(chǎn)物方面,國(guó)內(nèi)的企業(yè)通過(guò)技術(shù)引進(jìn)和自主創(chuàng)新,已經(jīng)可以解決副產(chǎn)物處理問(wèn)題,實(shí)現(xiàn)了物料的循環(huán)利用。有頭部企業(yè)利用甲醇制氫改電制氫、硅粉降耗、余熱回收制蒸汽、還原一鍵啟動(dòng)全過(guò)程控制等降耗減排措施,協(xié)同多晶硅還原智能控制平臺(tái),在高效生產(chǎn)的同時(shí),實(shí)現(xiàn)節(jié)能降耗,并大幅降低二氧化碳排放量。
但是流化床法的短板還真不是三兩下可以徹底解決的,畢竟流化床法也已經(jīng)誕生了60年。
第一,成品純度不高。前文講到,流化床反應(yīng)器內(nèi)的硅顆粒是處在懸浮狀態(tài),底部不斷有氣流進(jìn)入,“沸騰”的硅顆粒會(huì)不斷沖擊反應(yīng)器內(nèi)壁,長(zhǎng)時(shí)間運(yùn)作下,容易使反應(yīng)器內(nèi)部受到腐蝕,常用的金屬材料會(huì)給反應(yīng)體系帶入大量的金屬污染,降低產(chǎn)品純度。
光是這一點(diǎn),就讓流化床法的企業(yè)夠忙活一陣了。
一些企業(yè)也在研究使用石墨、碳化硅等材質(zhì)作為反應(yīng)器內(nèi)襯或涂覆在金屬壁面上,利用其高硬度、不會(huì)帶入金屬雜質(zhì)等優(yōu)勢(shì),杜絕此環(huán)節(jié)的金屬污染,但這會(huì)帶來(lái)增加投資成本。實(shí)際上,在西門子法和流化床法面世后的初期,當(dāng)時(shí)多晶硅市場(chǎng)需求主要為半導(dǎo)體行業(yè)用電子級(jí)多晶硅,流化床法因?yàn)榧兌冗_(dá)不到甚至一點(diǎn)機(jī)會(huì)都沒(méi)有。
第二,是第一點(diǎn)的延伸,反應(yīng)器內(nèi)壁不斷受到?jīng)_擊,容易帶來(lái)內(nèi)壁沉積硅粉,造成沾污,甚至造成噴嘴等關(guān)鍵部位堵塞,進(jìn)而使進(jìn)氣不均勻,不利于反應(yīng)。在內(nèi)壁沉積嚴(yán)重的情況下,仍然需要被迫停車進(jìn)行清理,甚至誘發(fā)反應(yīng)器內(nèi)壁的破裂。
結(jié)果就是目前流化床內(nèi)件的壽命只有半年到一年,跟還原爐超過(guò)20年的壽命比起來(lái)簡(jiǎn)直是快消品。舉個(gè)不是特別恰當(dāng)?shù)睦?,這就像你去買車,你是選動(dòng)力一般,但不容易壞的,還是選推背感十足,卻動(dòng)不動(dòng)要換零件的車。
第三,流化床對(duì)安全性的要求很高。硅烷易燃、易爆的突出特點(diǎn)和安全隱患,限制了硅烷流化床法的推廣使用。
從發(fā)展歷程上來(lái)看,上世紀(jì)70年代,美國(guó)聯(lián)合碳化合物公司,德州儀器公司等又開始對(duì)流化床生產(chǎn)工藝進(jìn)行研究,尤其是美國(guó)Ethyl公司(現(xiàn)為Sunedison)于1984年建廠生產(chǎn)電子級(jí)顆粒硅,但由于純度、成本等問(wèn)題,產(chǎn)能也未能進(jìn)一步放大。直到21世紀(jì)初,隨著光伏多晶硅需求的迅速增大,流化床法開始興起,但是至今未成規(guī)模。
流化床法見證了半導(dǎo)體和光伏的光輝歲月,卻毫無(wú)參與感可言。
一言以蔽之,理論的成本低和工業(yè)生產(chǎn)完全是兩碼事。比如電池最好的一定是氫燃料電池,但工業(yè)生產(chǎn)不具備經(jīng)濟(jì)性,流化床法的經(jīng)歷過(guò)往倒有點(diǎn)類似氫燃料電池,但是至今沒(méi)有成為主流,氫燃料電池作為鋰電池的補(bǔ)充,而氫能作為“終極能源”也是默默的當(dāng)光伏、風(fēng)電的備用能源。
雖然流化床法無(wú)法成為主流,但是顆粒硅憑借粒徑優(yōu)勢(shì),不需要破碎可直接使用,能填補(bǔ)硅塊間的空隙提高坩堝裝填量,提高拉晶產(chǎn)出,可以作為改良西門子法的補(bǔ)充。
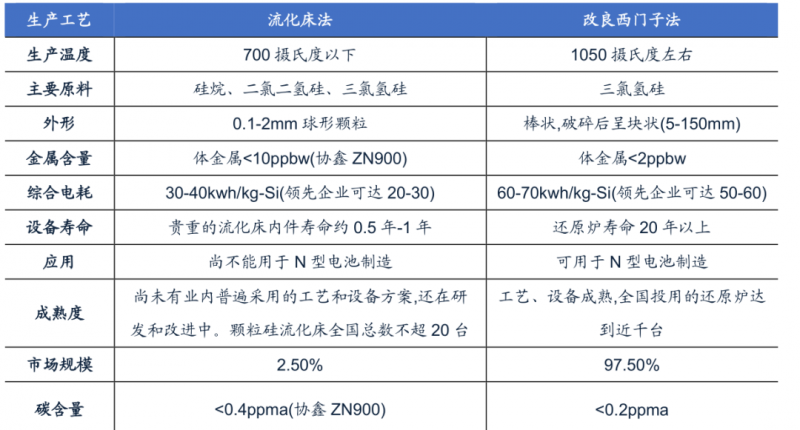
圖10:西門子法和流化床法的優(yōu)劣勢(shì)比較,資料來(lái)源:亞洲硅業(yè)科創(chuàng)板上市申請(qǐng)文件的審核問(wèn)詢函回復(fù),廣發(fā)證券
03
多晶硅企業(yè)用腳投票
對(duì)于技術(shù)路線的選擇,全球頭部企業(yè)的擴(kuò)產(chǎn)情況已經(jīng)給了大眾一份答案,本文做下總結(jié)。
【1】穩(wěn)定供貨的能力
多晶硅的穩(wěn)定供應(yīng)是光伏發(fā)展的重中之重。
一方面是產(chǎn)品的穩(wěn)定供貨,在供應(yīng)緊張的情況下,擴(kuò)產(chǎn)是主旋律。根據(jù)國(guó)金證券的統(tǒng)計(jì),2022年國(guó)內(nèi)主流硅料企業(yè)的90%以上產(chǎn)能均已被下游長(zhǎng)單鎖定,且最新的硅料長(zhǎng)單已經(jīng)簽至2026年,未來(lái)幾年高比例長(zhǎng)單將成為硅料行業(yè)的常態(tài)。
另一方面,指的是產(chǎn)品質(zhì)量的穩(wěn)定性,多晶硅更多的是化工品屬性,因此產(chǎn)品的穩(wěn)定性是最重要的考量,沒(méi)有之一。這自然涉及到生產(chǎn)的工藝的穩(wěn)定性、設(shè)備的穩(wěn)定性。改良西門子法工藝成熟穩(wěn)定,設(shè)備也非常成熟,全國(guó)投入使用的還原爐達(dá)到近千臺(tái),遠(yuǎn)超流化床(全國(guó)流化床總數(shù)不超過(guò)20臺(tái))。
【2】長(zhǎng)周期視角下,西門子法仍具明顯的降成本空間
西門子法未來(lái)仍具有明顯的降成本空間,我們從幾個(gè)方向做初步討論:
1)加大還原爐尺寸
說(shuō)白了就是進(jìn)一步提升規(guī)模效應(yīng)。西門子法中,還原爐產(chǎn)量已從1975年的單爐40噸/年,提升至2015年的500噸/年。隨著還原爐單爐產(chǎn)能的繼續(xù)提高和電耗的繼續(xù)降低,推動(dòng)改良西門子法繼續(xù)成為多晶硅行業(yè)發(fā)展的主導(dǎo)技術(shù)。
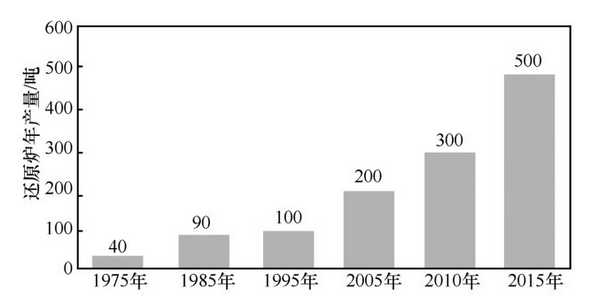
圖11:不同年代的主流還原爐年產(chǎn)量情況,資料來(lái)源:公司公告
2)還原爐新型材料的應(yīng)用
還原爐材料從石英玻璃發(fā)展到不銹鋼,未來(lái)通過(guò)使用不銹鋼以外的新型材料,或者給內(nèi)壁鍍上反射膜等方式,提高熱輻射能的反射率,以提高余熱利用率,此方式可實(shí)現(xiàn)10%~20%的節(jié)電效果,但相應(yīng)對(duì)內(nèi)壁的材質(zhì)也提出較高要求,須考慮材質(zhì)的耐用性及成本問(wèn)題。
3)閉環(huán)生產(chǎn)
由于改良西門子法生成的副產(chǎn)物和尾氣較多,影響到生產(chǎn)成本。如何有效循環(huán)和處理產(chǎn)物關(guān)系到未來(lái)的降本方向。比如西門子法生產(chǎn)過(guò)程中會(huì)產(chǎn)生大量的副產(chǎn)物SiCl4,將SiCl4轉(zhuǎn)化成作為多晶硅生產(chǎn)原料的SiHCl3,從而實(shí)現(xiàn)閉環(huán)生產(chǎn),以提高硅粉利用率,降低生產(chǎn)成本。
總之,改良西門子法由于規(guī)模化、技術(shù)成熟,未來(lái)有進(jìn)一步的下降空間。絕大部分企業(yè)仍選擇采用改良西門子法進(jìn)行擴(kuò)產(chǎn)。正是基于以上認(rèn)知,CPIA(中國(guó)光伏)估算,到2030年,用改良西門子法生產(chǎn)的多晶硅,仍是絕對(duì)的主流。本文開篇提出的問(wèn)題,對(duì)應(yīng)的答案也就躍然紙上了。
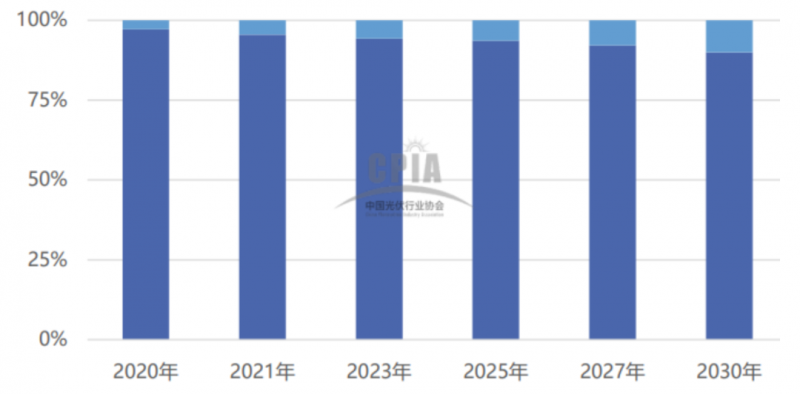
圖12:國(guó)內(nèi)西門子法(深藍(lán))和顆粒硅(淺藍(lán))占比,資料來(lái)源:CPIA,華安證券
評(píng)論